Brake Pads Manufacturer since 2012
We are not only the manufacturer of brake pads, but also your partner to increase your revenue and make your brand greater. Let Hyperolls do something different with you.
The Brake Pads We Produce
The clutch Linings, also named clutch facings, are the most important components in the manual-operated automobiles; it is a part of the clutch disc. There are many types of clutch linings with different materials, such as glass fiber clutch linings, core-spun yarn clutch linings, composite yarn clutch facings, aramid clutch facings, and carbon fiber clutch facings. As a professional manufacturer of clutch linings with more than 20 years of experience, Hyperolls is able to provide most of the clutch facings you need.
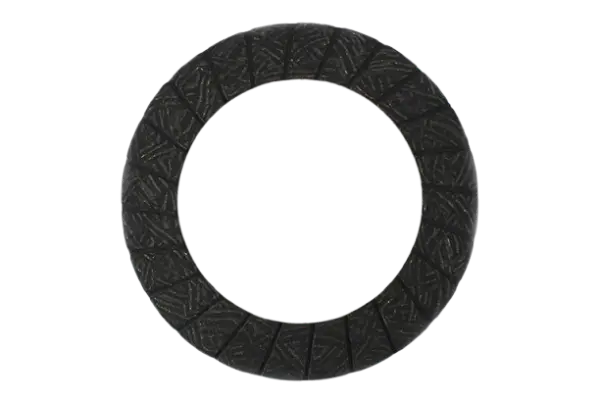
Glassfiber Clutch Lining
Model H1209
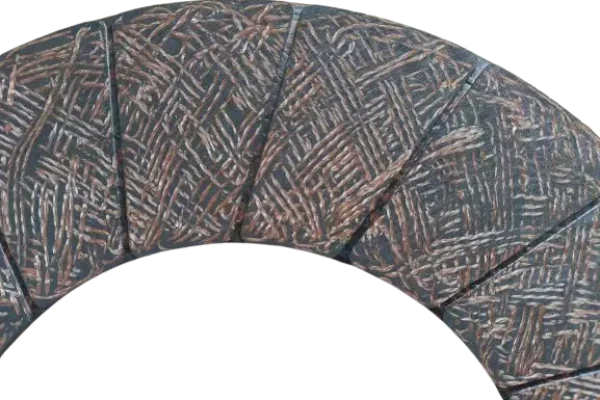
Glassfiber Clutch Lining
Model H1212
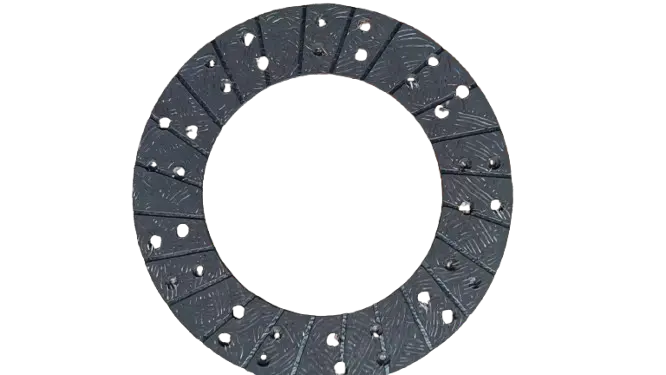
Core-spun Yarn Clutch Lining
Model H2458
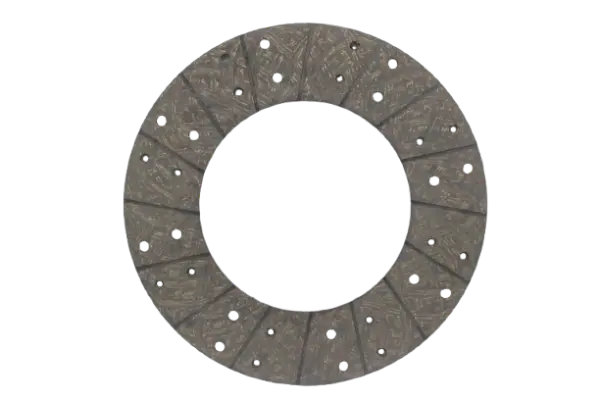
Composite Yarn Clutch Facing
Model H3115
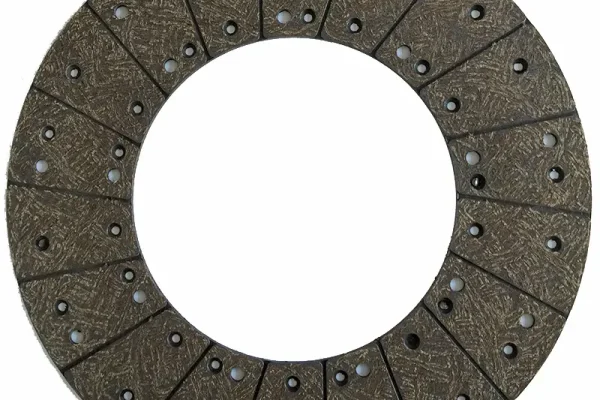
Aramid Clutch Facing
Model H6492
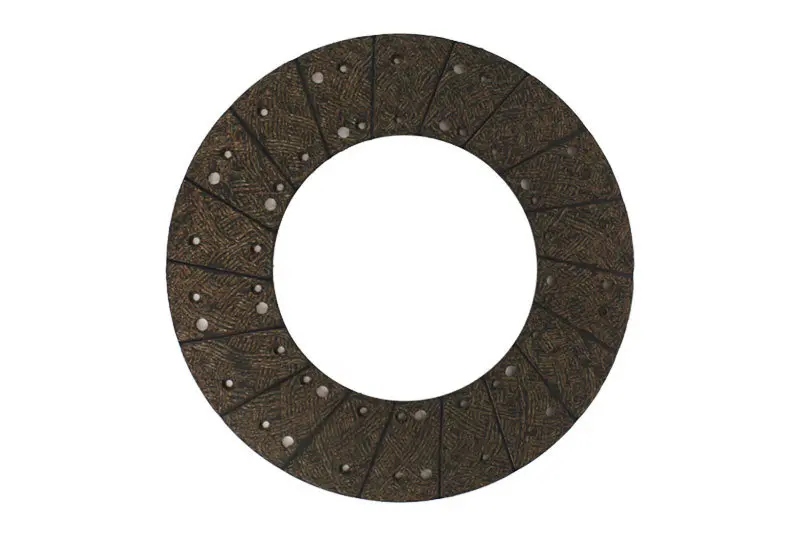
Carbon Fiber Clutch Facing
Model H8008
Let's Talk About Your Needs In Clutch Linings
What are Clutch Linings?
Clutch Linings, also known as clutch facings, are circular friction discs that are riveted onto the driven clutch disc. Typically, two clutch linings are installed on each driven clutch disc. Their primary function is to transfer power from the engine to the transmission, enabling the vehicle to move efficiently.
The clutch linings are made from safer and more durable materials such as metals, glass fibers, organic compounds,core-spun yarn, composite yarn, and aramid fibers (e.g., Kevlar). These materials provide excellent performance, heat resistance, and environmental safety.
Clutch facings are manufactured through a multi-step process, including: yarn spinning, rubber coating, skeleton winding, heat compression molding, and surface finishing. Each clutch lining undergoes a strict quality inspection to ensure reliability and performance. Only approved pieces are packaged according to customer requirements.
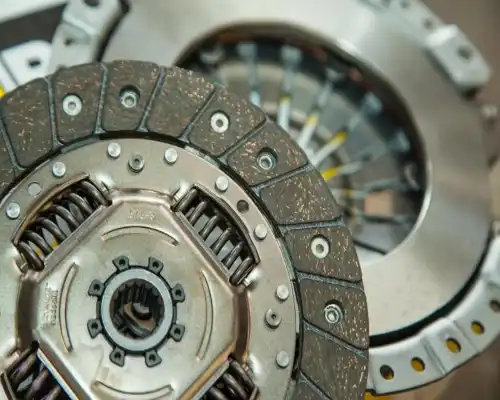
√ Glass Fiber
√ Core-spun Yarn
√ Composite Yarn
√ Aramid Fiber
√ Carbon Fiber
√ Copper Wire
√ Friction Material
√ Resin
√ Rubber Adhesives
A Wide Range Of Excellent Materials
The quality of the clutch linings is determined by the characteristics of the different materials. Metals are wear-resistant and temperature-resistant, but their high hardness can damage the counterpart. Organic composite materials are wear-resistant and stable, but their hardness is not high, and their friction coefficient is low. Through the combination of different materials to form clutch facings for different car models and regions, it is a good solution to the requirements of wear resistance, high temperature resistance, and long-lasting power transmission. Our R&D team has developed a variety of best-selling clutch facings by testing different formulas. The left side is our commonly used material, which has been proven to have good characteristics.
The Specifications and Unique Features
Specifications
Items | Values | Standard |
Density | 1.9±0.1g/cm³ | GB/T4472 |
Friction coefficient | ≥0.42 | GB 5763-2008 |
Wear rate | ≤0.18x10cm³/Nm | GB 5763-2008 |
Impact strength | ≥0.35 J/c㎡ | GB/T1043.1 |
Rockwell hardness | ≥50 | GB 5766 |
Compressive strength | ≥60Mpa | GB/T1041 |
Unique Features & Benefits
Our clutch facing is made of high-quality organic fiber and a copper wire skeleton composed of materials, high-temperature resistance resins, and rubber adhesives. With the high-performance formulas and crafted production process, the clutch linings are in stable friction coefficient, low wear rate, and high impact strength. The variety of our clutch linings can meet most of the vehicles worldwide.
Features Include:
- Stable friction coefficient
- High-temperature resistance
- Low wear rate
- High impact strength
- High compressive strength
Other Advantages:
- High density
- Different colors
- Low tolerance
- Low MOQ
- Wide Type range
- Durability
- Fast shipment
Dimensions Table
We provide the outer diameter from 100mm to 450mm, and more than 1000 models are available, covering passenger cars, trucks, and other vehicles made in China, Europe, Japan, Korea, and America.
No. | Outer Dia.(mm) | Inner Dia.(mm) | Thickness (mm) |
1 | 170 | 110 | 3.5 |
2 | 180 | 125 | 3.5 |
3 | 190 | 135 | 3.5 |
4 | 200 | 140 | 3.5 |
5 | 210 | 150 | 3.5 |
6 | 215 | 150 | 3.5 |
7 | 225 | 150 | 3.5 |
8 | 240 | 160 | 3.5 |
9 | 250 | 165 | 3.5 |
10 | 260 | 170 | 3.5 |
11 | 275 | 170 | 3.5 |
12 | 280 | 170 | 3.5 |
13 | 295 | 170 | 3.5 |
14 | 300 | 190 | 3.5 |
15 | 310 | 170 | 3.5 |
16 | 325 | 190 | 3.5 |
17 | 350 | 190 | 3.8 |
18 | 380 | 200 | 3.8 |
19 | 420 | 220 | 3.8 |
20 | 430 | 235 | 3.5 |
21 | 430 | 235 | 3.8 |
What Industries Use Clutch Linings
Clutch linings are not only used in automobiles, but also in a wide range of industries. Here are some examples of industries that use clutch linings.
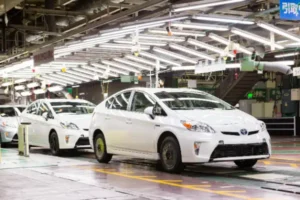
Automobile
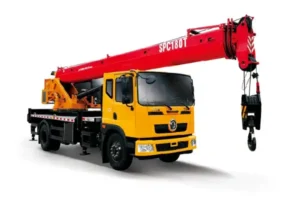
Contruction Machine
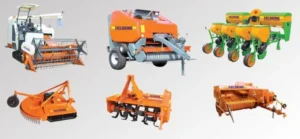
Agriculture Machine
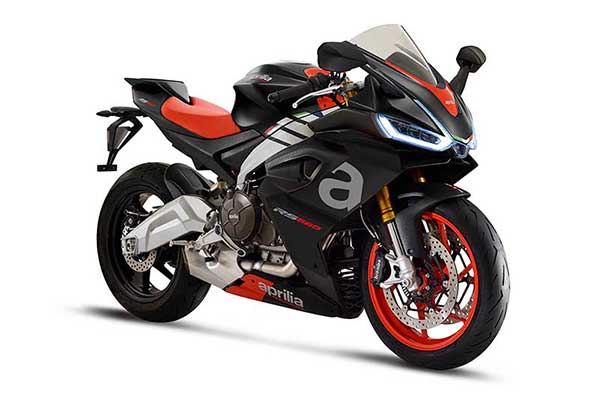
Motorcycles
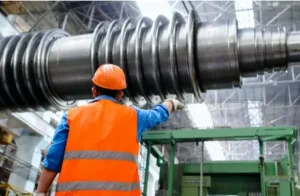
Industrial Equipment
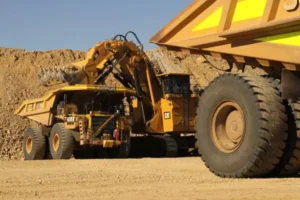
Mining Machine
How to Spot Signs of Clutch Facing Failure
The clutch facing can wear out, leading to performance issues and potential failure of the clutch system over time. Recognizing the signs of a failing clutch facing early can save you time and money. Below are five key symptoms to watch for.
Vibration When the Car Starts
If your car shakes or vibrates when you start it and press the clutch pedal, it could indicate a problem with the clutch facing. This jittery feeling often means the clutch facing or pressure plate is worn out. A healthy clutch facing should allow for smooth engagement without any shuddering. Catching this early can prevent bigger problems down the road.
Abnormal Noise When Engaging a Gear
Hearing grinding, squealing, or whining noises when shifting gears? These sounds can point to a worn clutch facing, a faulty release bearing, or flywheel issues. A properly functioning clutch facing should operate quietly, so unusual noises are a clear signal something’s wrong.
Peculiar Smell When Driving
A strange burning smell, especially after heavy clutch use—like in traffic or on hills—could mean the clutch facing is slipping or overheating. This odor often comes from the clutch facing rubbing against the flywheel due to wear. If you notice this, don’t ignore it; it’s a sign of damage.
Slipping After Engaging a Gear
Does your engine rev up without the car speeding up? That’s a sign of clutch facing slipping. It happens when the clutch facing is too worn to grip the flywheel properly, reducing power to the wheels. This common symptom of clutch facing failure needs quick attention to avoid getting stranded.
Underpowered When Driving
If your car feels sluggish, especially when accelerating or climbing hills, the clutch facing might be failing. This occurs when the clutch facing doesn’t fully engage, limiting power transfer to the wheels. Don’t mistake it for an engine issue—check the clutch system if the vehicle lacks its usual pep.
Spotting these symptoms of clutch facing failure—vibration, odd noises, burning smells, slipping gears, or low power—can help keep your vehicle running smoothly. If you notice any of these, get it checked by a mechanic promptly to avoid bigger issues.
Why Choose Hyperolls As Your Partner
Choose a reliable supplier of clutch linings, not only save your money and time, but also increase your profit with relaxation and efficiency.
Wide Product Range
Over 200 kinds of clutch facing formular, covers all major vehicle and machinery types
Full Customization
Tailored formulations, sizes, and branding options make your different
Competitive Prices
Cost-saving patented materials and optimized production process cut unnecessary costs
Fast And Safe Delivery
15-day standard production and global express shipping options
Military-Grade QC
Triple-inspection system with batch test reports, we regard safe as first
Industry-Best Warranty
We provide super long of 24-month coverage (vs. standard 12 months)
How to Make Your Clutch Facing Last Longer?
To extend the lifespan of your clutch facings, adopt driving habits and maintenance practices that reduce wear and tear. Below are seven key and workable tips to help you maximize the durability of your clutch facings, ensuring smoother performance and fewer costly repairs.
Minimize Clutch Riding
Avoid keeping your foot on the clutch pedal unnecessarily, as this causes partial engagement and accelerates wear on the clutch facings. For example, when stopped at a traffic light, shift into neutral and release the clutch fully to prevent undue strain. Resting your foot lightly on the pedal, even unintentionally, can create enough pressure to cause slippage, heating up the clutch and wearing it down prematurely.
Engage the Clutch with Care
Practice smooth and deliberate clutch engagement to reduce stress on the clutch facings. When shifting gears, press the clutch pedal fully to the floor, shift smoothly, and release the pedal gradually while coordinating with the accelerator. Jerky or rushed movements can cause the clutch to slip or grind, wearing out the facings faster. Over time, this technique becomes second nature and significantly extends clutch life.
Avoid Overloading Your Vehicle
Carrying excessive weight puts extra strain on the clutch, as it requires more force to engage and disengage gears. Stick to your vehicle’s recommended load capacity, and avoid towing loads beyond its capability. For instance, if you’re transporting heavy cargo or passengers, plan routes with fewer stops and starts to reduce clutch usage, as frequent engagements under heavy loads accelerate wear.
Drive Cautiously in Adverse Weather
Inclement weather, such as heavy rain, snow, or mud, can make clutch operation more demanding. Wet or slippery conditions may tempt you to ride the clutch for better control, but this wears the facings faster. Instead, use lower gears for better traction and maintain steady speeds. If possible, avoid driving in severe weather, or plan routes with less demanding conditions to protect your clutch.
Use the Handbrake on Hills
When starting on an incline, rely on the handbrake to hold the vehicle instead of balancing with the clutch and accelerator. Holding the clutch at the “biting point” to prevent rolling back generates heat and wears the clutch facings rapidly. Engage the handbrake, release the clutch fully, and then use the handbrake release in coordination with smooth clutch engagement to start moving. This technique reduces clutch strain and preserves its lifespan.
Cultivate Smooth Driving Habits
Refine your driving style to minimize aggressive maneuvers that stress the clutch. Avoid unnecessary downshifting (e.g., shifting from fifth to second gear when third would suffice), skipping multiple gears, or revving the engine excessively before engaging the clutch. Instead, shift sequentially and match engine speed to gear selection. Smooth driving not only extends clutch life but also improves fuel efficiency and overall vehicle performance.
Prioritize Regular Clutch Maintenance
Schedule periodic inspections with a qualified mechanic to catch early signs of clutch wear, such as slipping, unusual noises, or a spongy pedal feel. Regular maintenance includes checking the clutch fluid (in hydraulic systems), adjusting the clutch cable (if applicable), and ensuring the clutch components are properly lubricated. Addressing minor issues promptly prevents excessive wear on the facings and avoids costly repairs down the line.
By following these tips, you can significantly prolong the life of your clutch facings, ensuring a smoother and more reliable driving experience.
Have a Question?
We're Here to Help!
- +86 1 3665 3910 03